Not enough hours in the day?
It is not unusual to get into Q3 and find that you simply won’t be able to get through that long list. We had a recent experience where one of our clients had a list of 57 items that were either necessary, or would be nice to do. There’s a 5 year plan in place, with Health & Safety driven items obviously a priority. No doubt that, over the 5 year period, priorities will change and some items will be superseded, however, in between the list being released, and a short list being prepared, it became clear that a major changeover was required, meaning that all the internal engineering resource was allocated to this instead.
The outcome?
In terms of Capex spend, the client is pretty much where they started, give or take a few small vital elements.
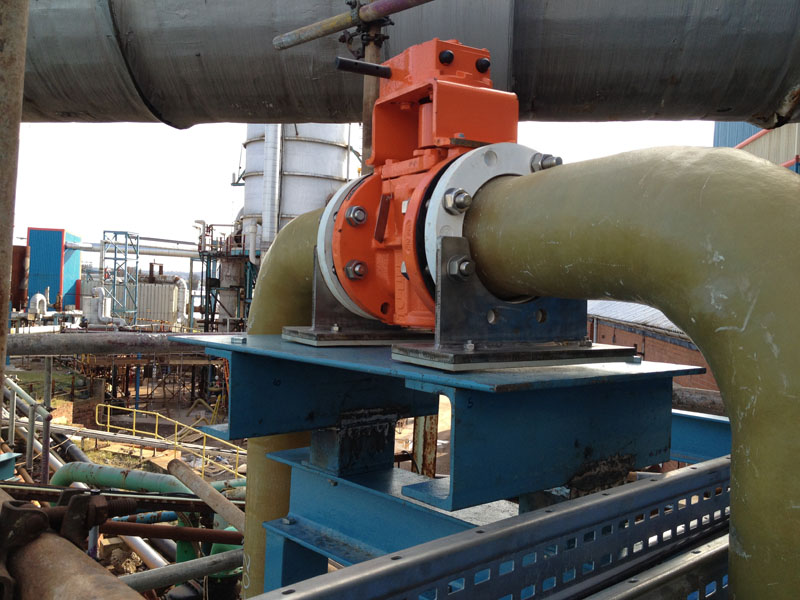
How can Addison help?
Assuming that you’ve already prepared your Capex budget, and got the go ahead, we’ll then propose what is, effectively, a 4 step plan.
- Understand exactly what you need to do during the next year.
- Do you have a priority for any reason (ie H&S, Process Improvements, Energy Reduction)?
- Once the priorities are decided, do you have firm costs? If not, how do you intend to get these costs, do you need to do any design work?
- Plan. How do you intend to get the work done, can you handle the design, planning, execution?
- Project Management – do you have the resources to do this in house? If not, does your budget extend to using on outside contractor?
The last question, interestingly, is pretty much where you need to start. This is where our capabilities come in.
What can Addison actually do for your site?
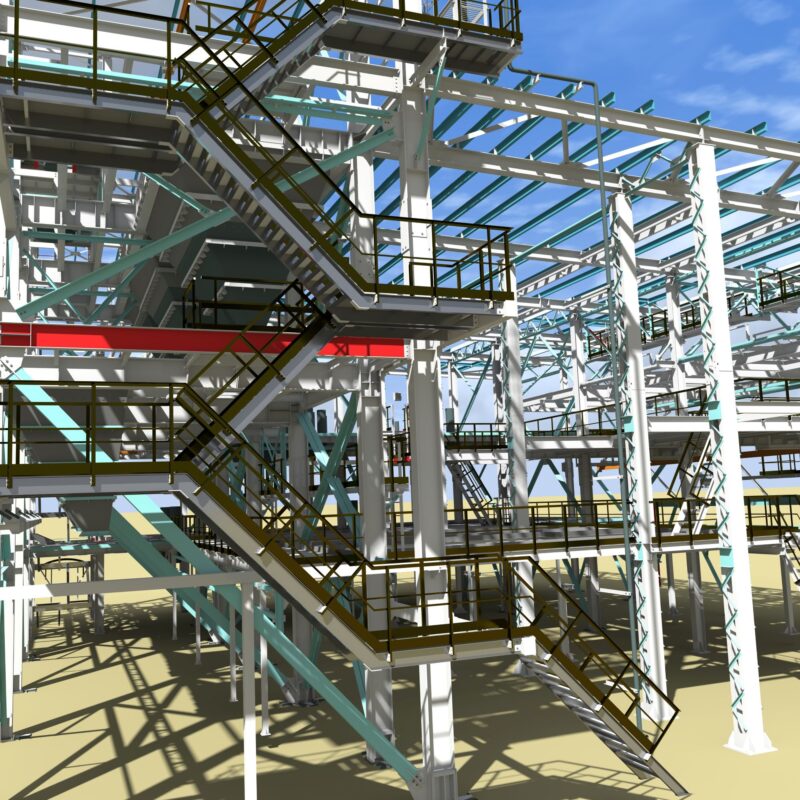
At some point during your Capex programme, you are going to need to stop production. Minimising the duration of an outage can have a major impact in reducing the cost of lost production.
Addison Project process technical services can provide qualified and experienced personnel to augment the resources available to handle shutdown planning and scheduling, manage the shutdown activities and assist in the start-up of the facilities to minimise the out-of-service time.
Shutdowns can be costly in terms of lost production, so a carefully designed plan can reduce costs. In many respects a shutdown can be even more complicated than the initial construction of the facility. Not only must the facility in the end be reassembled and the work carefully reviewed before start-up, as it was when construction was completed, it must first be shutdown, cleaned up and partially disassembled in order to restore its original functionality. Consideration must be given to the impact on both upstream and downstream processes, and the impact on customers and suppliers.
Dependent on the size of plant and requirements from the shutdown, planning should begin well in advance before the anticipated shutdown is to take place. Our approach is informed from the successes and failures of the past shutdowns and incorporates the necessary improvements to make it a success. It goes without saying this process involves input from lots of different interfaces, including procurement, engineering, maintenance and operations.
Shutdown planning is led by engineers who are not only familiar with the appropriate planning tools, MS Project and Primavera, but are also experienced in on site engineering works and are for that reason are able to co-ordinate and manage the various interfaces accordingly.
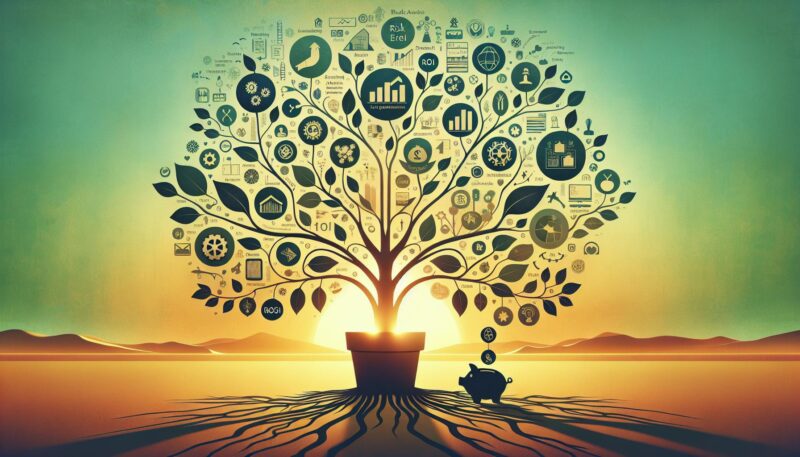
Respect the Process
We’ve talked before about how to run a project efficiently. Capex work fits this bill exactly. If you wish to discuss anything related to your programme, please contact us.
Due to the support we can offer from all 3 offices, we can help you right now.