Laser scanning records and transfers the survey area into a digital computer format that can be analysed remotely. It captures the shape of any physical object allowing measurements to be taken easily and is commonly used to accurately capture and store “as-built” or “existing” information, often from safe remote locations, to assist the design process.
As well as providing a fly through view of any structure or building it can also generate plan and section views. Combining this with the known relative densities of each point allows an image or mesh to be superimposed over the top of the point cloud to create a reconstruction.
After scanning a site or building, the information can be exported onto the Internet for use with Leica’s TruView technology. This will allow any third party to have access to the 3D scan without the need for expensive software. From the TruView environment measurements can be taken and engineers can work together on the same project from various locations.
Civil engineers, plant designers, CAD professionals, architects, contractors, owners and operators can all reap the cost and added value benefits that our surveying provides.
Ensuring Constructability, Maintainability & Operability
The use of 3D laser scanners allows you to add value to your project in a cost effective way. Some of the benefits of this technology includes:
- Lower cost as-built drawings and topographical surveys
- Elimination of costly ‘return visits’ to the site
- More accurate and complete, creating less construction rework
- Reduced facility downtime due to fast, unobtrusive scene capture and minimal field fit-up, field fabrication and field rework
- Inaccessible locations can now be safely surveyed without the need for costly scaffolding or the use of cherry pickers
- Faster and better quality results
- Shorter project cycle times
- Higher level-of-detail and safer, unobtrusive data capture
- Point clouds can be conveniently used and reviewed by others for more efficient management of projects
Mitigate your Project Risk
- Verification of design against ‘as built’ condition.
- Clash detection.
- Vendor product verification prior to delivery.
- Pre planning critical construction tasks e.g. heavy lifts and installation
routing simulation.
- Audit construction progress, resource and material utilisation.
Document and Analyse Critical Assets
- Update existing plant records
- Vessel deformation monitoring and analysis.
- Infrastructure condition reporting.
- Maintenance planning.
- Asset management software integration
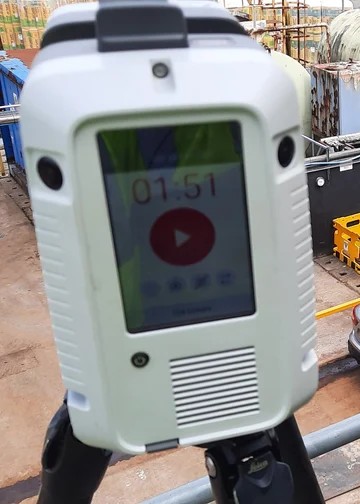